雙堿法煙氣脫硫技術
技術簡介
雙堿法煙氣脫硫技術是為了克服石灰石—石膏法容易結垢的缺點而發展起來的。傳統的石灰石/石灰—石膏法煙氣脫硫工藝采用鈣基脫硫劑吸收二氧化硫后生成的亞硫酸鈣、硫酸鈣,由于其溶解度較小,極易在脫硫塔內及管道內形成結垢、堵塞現象。結垢堵塞問題嚴重影響脫硫系統的正常運行,更甚者嚴重影響燒結機系統的正常運行。為了盡量避免用鈣基脫硫劑造成結垢堵塞問題,同時單純采用鈉基脫硫劑運行費用太高且脫硫產物不易處理的問題,雙堿法煙氣脫硫工藝應運而生,該工藝較好的解決了上述問題。
雙堿法是先用可溶性的堿性清液作為吸收劑吸收SO2,然后再用石灰乳或石灰對吸收液進行再生,鈉鈣雙堿法是以碳酸鈉或氫氧化鈉溶液為第一堿吸收煙氣中的SO2,然后再用石灰或熟石灰作為第二堿,處理吸收液,再生后的吸收液送回吸收塔循環使用。由于采用鈉堿液作為吸收液,有效克服結垢和漿料堵塞問題,且鈉鹽吸收速率比鈣鹽速率快,所需要的液氣比低很多,可以節省動力消耗。鈉鈣雙堿法在國外(如日本、美國)已成功實現大型化應用,在日本和美國至少有50套雙堿法脫硫裝置,成功應用于電站、工業鍋爐及燒結機,國內已有多套成熟的工程應用業績。
技術原理
雙堿法主要以碳酸鈉或氫氧化鈉溶液作為脫硫劑吸收煙氣中的SO2,然后再用石灰乳或石灰對回收液進行再生。
脫硫劑中的碳酸鈉或氫氧化鈉與SO2、SO3、HF、HCL等發生化學反應,生成亞硫酸鈉和亞硫氫酸鈉等物質,脫硫后的凈煙氣通過除霧器除去氣流中夾帶的霧滴后排出吸收塔。反應后的脫硫劑進入再生池,與從石灰漿液池過來的石灰漿液發生再生反應,生成脫硫副產物,脫硫副產物沉積后排出,壓濾成石膏。上清液流經泵前池,經沉淀后循環水泵抽送到脫硫裝置進行脫硫循環。
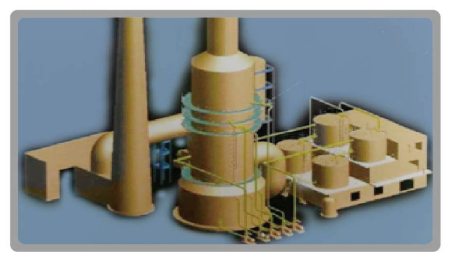
雙堿法脫硫技術結構示意圖
工藝流程
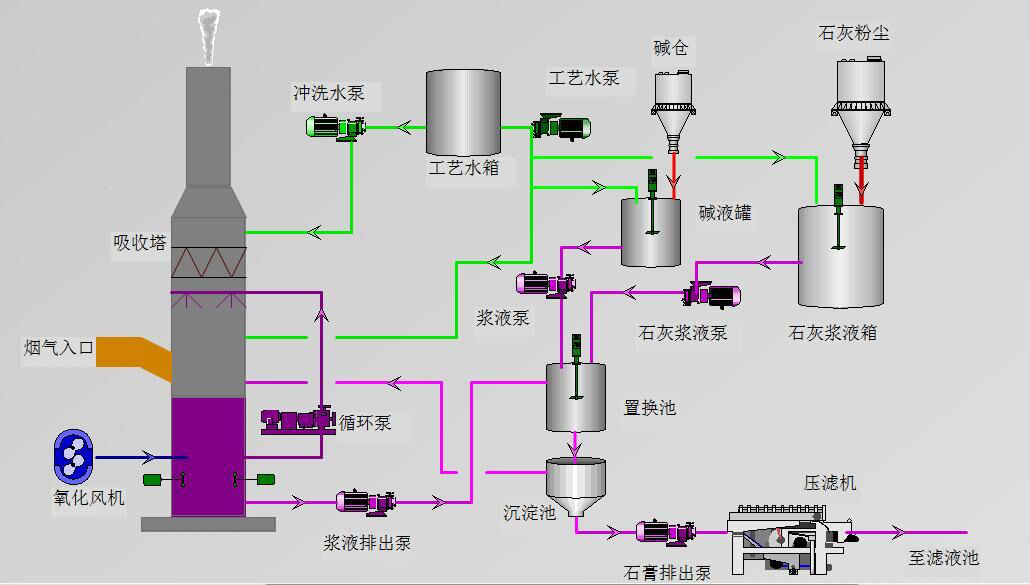
雙堿法煙氣脫硫技術——工藝流程圖
技術特點
雙堿法具有“三高、二低、一小”的特點:即:脫硫效率高、可利用率高、可靠性高;投資成本低、運行費用低;占地面積小。
1. 脫硫效率高:雙堿法采用鈉堿做為吸收劑,由于鈉堿的堿性強、溶解度大、反應活性遠大于石灰石/石灰,所以只用很低的液氣比就可達到高效率的脫硫效果,對高硫煙氣處理效果更明顯。
2. 可利用率高:鈉堿吸收SO2后,通過鈣基強堿的置換,鈉堿循環使用,每小時只需補充少量的鈉堿即可保證系統鈉離子濃度平衡,整個系統的鈉堿濃度及PH值在合理可控的范圍內,同時由于置換反應是速度極快的離子反應,因此可以有效利用鈣基脫硫劑,整體Ca/S為1.01~1.03。
3. 可靠性高:雙堿法技術成熟,運行穩定可靠,最大的是美國Central Illinois Public Service,Newtown 1#,575MW鍋爐,目前,雙堿法在國內也有多套裝置在運行,運轉實踐證明,該工藝流程簡單可靠,主要設備故障率低,對煙氣變化的適應性強,可根據燒結礦的變化,適當調節pH值、液氣比等因子,以保證設計脫硫率的實現。
4. 投資成本低:與其他濕法脫硫工藝相比,鈉鈣雙堿法工程投資相對較低;脫硫效率同樣達到90%~95%,脫硫后的SO2和煙塵排放完全滿足環保要求。
5. 運行費用低:由于雙堿法的液氣比較小,故循環漿液量也很小,因此可以有效降低循環泵的電力消耗,同時Ca/S也很小,可以有效節省脫硫劑消耗,降低業主的運行成本。
6. 占地面積小:該系統布置靈活,系統所需設備也小于其他濕法脫硫工藝,整套脫硫裝置可以根據場地情況合理布局,有效節省占地面積。
適用范圍
適用于火電廠、燒結、球團、焦化、水泥、玻璃等行業。